Cost to Install a Bay Window
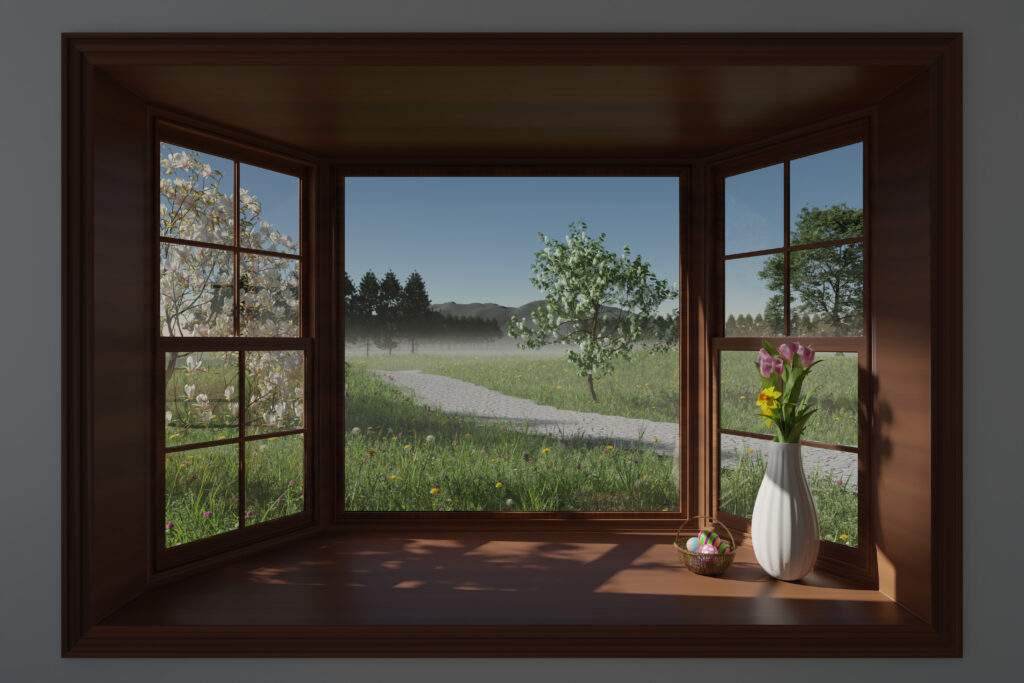
Upgrading to a bay window can dramatically improve both the look and feel of a room, but it’s also a project with wide-ranging cost considerations.
Bay windows are a distinctive window style that extends beyond a home’s exterior wall, creating a multi-angled alcove that adds both visual interest and functional space. Typically composed of a large central pane flanked by two angled side panes, bay windows bring in more natural light than flat windows and open up interior rooms without increasing the home’s footprint. They’re often used to create built-in seating, breakfast nooks, or display shelves, making them a popular upgrade in living rooms, kitchens, and bedrooms.
Understanding what drives the cost of bay window installation can help you budget effectively and choose the right configuration for your space. Here’s a detailed look at what to expect.
Table of Contents
National Average Cost Overview
Installing a bay window in the U.S. generally costs between $2,000 and $4,000 per unit, with a national average of around $2,500 to $3,600. Prices vary depending on size, material, labor, and whether the project involves replacement or new installation. Homeowners seeking basic models may spend as little as $1,000, while custom designs with premium finishes can exceed $7,500.
Breakdown of Cost Factors
Size and Complexity
Window size and installation complexity are major pricing drivers. Larger or more elaborate windows involve more materials and labor. Most bay windows cost between $100 and $150 per square foot installed. Typical size-based estimates include:
- 4 ft by 3 ft window: $1,400
- 5 ft by 4 ft window: $2,500
- 6 ft by 8 ft window: $7,500
Structural changes such as reframing or second-story installation can significantly raise costs.
Materials and Styles
Material choice directly affects cost, durability, and appearance. Common frame materials include:
- Vinyl $700 to $3,500, affordable and low maintenance
- Wood $1,100 to $6,000, offers traditional style but needs upkeep
- Fiberglass $900 to $4,500, durable and energy efficient
- Aluminum $500 to $2,200, less energy efficient
- Steel $1,600 to $7,000, highly durable but costly
Bay windows are available in several styles, each with distinct cost implications:
- Box Square design, most affordable option
- Canted (Angled) Common residential style, moderate cost
- Oriel Suspended from the wall, usually for upper floors
- Circle Curved bay windows, higher cost due to custom work
Labor and Installation
Labor generally makes up 40 to 60 percent of the total installation cost. Typical professional labor charges range from $1,000 to $1,500 per window. Labor costs rise when additional structural work is required, such as cutting a new opening or reinforcing the wall. Second-floor installations and projects requiring roof modifications are more complex and expensive. Homeowners should also factor in demolition, cleanup, and finishing services.
Additional Services
Some bay window installations require auxiliary services, which can add to the total project cost:
- Structural engineer evaluation approximately $550
- General contractor supervision $250 to $500
- Drywall repair and trim finishing varies by scope, typically $300 to $800
- Permit fees $50 to $250 depending on municipality
These services are often necessary for load-bearing walls or when expanding the window opening.
New Installation vs Replacement
Replacing an existing bay window is generally less expensive than installing one in a new location. Replacements cost about $1,800 to $2,500, depending on material and labor. New installations are more costly due to the need for structural changes, which may include cutting into the wall, reframing, siding, and finishing work. Additional expenses often apply for insulation, painting, or weatherproofing the newly modified exterior.
Cost Saving Strategies
There are several practical ways to reduce bay window installation costs:
- Choose spring or fall installation for better contractor availability and pricing
- Opt for vinyl or fiberglass frames to balance performance and affordability
- Avoid high-end custom shapes unless required by design
- Request detailed quotes to separate material and labor charges
- Compare at least three contractor estimates before committing
DIY installation can reduce costs by 10 to 15 percent but comes with risks. Improper installation may lead to water infiltration or building code violations.
Return on Investment and Value
Bay windows contribute to property value by enhancing curb appeal and increasing interior natural light. They can also make rooms feel larger and more inviting, which appeals to prospective buyers. According to industry estimates, homeowners can expect to recoup up to 70 percent of the installation cost when selling the home. In comparison to other window types, bay windows generally provide higher functional and visual return, though they are more expensive than casement or picture windows.
Quick Cost Calculator
Estimating the cost of a bay window installation involves several variables. A basic formula includes:
- Select window size and calculate square footage
- Multiply by average installed cost per square foot ($100–$150)
- Add material-specific premiums (wood, fiberglass, etc.)
- Include labor (40–60 percent of subtotal)
- Factor in extras such as permits, finishing, or structural changes
A 5 ft by 4 ft vinyl bay window installed professionally might cost:
- Size 20 sq ft × $125/sq ft = $2,500
- Labor ~ $1,200
- Permit and trim work ~ $400
- Total: Approximately $4,100
Expert Tips Before You Buy
Installing a bay window involves more than just selecting a style or material. It’s a structural upgrade that affects your home’s energy performance, resale value, and long-term maintenance. Taking the time to plan the project thoroughly can help you avoid unexpected costs and ensure a high-quality result.
Get Multiple Quotes from Licensed Contractors
Start by obtaining at least three quotes from local contractors with proven experience in window installation. Ask for references and check online reviews or ratings through licensing boards or trade associations. Verifying that a contractor is licensed and insured protects you from potential liability and ensures the work meets local building standards.
Different contractors may offer different installation approaches or timelines, so comparing bids also helps you understand market rates and scope variations.
Request a Line-Item Breakdown
Avoid lump-sum estimates. Instead, ask each contractor for a detailed, line-item breakdown of costs. This should include separate pricing for the window unit, labor, permits, finish work, and any structural modifications.
A transparent estimate allows you to see where your money is going and makes it easier to compare quotes accurately. It also helps you identify potential upsells or hidden costs, such as cleanup fees or charges for debris disposal.
Confirm Permits and Code Compliance
Most bay window installations, especially new openings or structural modifications, require a building permit. Your contractor should handle this process and be familiar with your local code requirements, including minimum insulation values, safety glass rules near floors, and setback distances for exterior projections.
Before signing a contract, ask for written confirmation that all necessary permits will be obtained and that the work will meet or exceed local code standards. Unpermitted work can cause problems during home resale or insurance claims.
Ask About Warranties
Reliable contractors and reputable manufacturers typically offer warranties on both the product and the workmanship. Ask for the details in writing. A manufacturer’s warranty may cover defects in materials for 10 to 20 years, while a contractor’s warranty may cover labor for one to five years.
Ensure the warranty includes protection against issues like water intrusion, seal failure, or frame warping. Clarify who will be responsible for filing a claim and what documentation you should keep after installation.
Prioritize Energy Efficiency
Bay windows introduce more glass surface area, which can affect heating and cooling efficiency. Look for products certified under the ENERGY STAR program. These windows meet strict criteria for U-factor, solar heat gain coefficient (SHGC), and insulation performance based on your region.
Choosing energy-efficient glass with low-emissivity (Low-E) coatings, gas fills (like argon), and proper thermal breaks can significantly reduce energy loss. While these features may cost more upfront, they can lower utility bills and increase comfort over the window’s lifespan.
FAQs
Do bay windows increase home value?
Yes, bay windows can significantly increase a home’s resale value. These windows are considered a high-impact architectural upgrade that appeals to many prospective buyers. They add depth to exterior walls and create inviting interior spaces filled with natural light. When staged correctly, a bay window area can make a room feel larger, brighter, and more attractive.
The value increase will depend on the type of window installed, the quality of the materials, and how well the addition blends with the home’s architectural style. High-end materials like wood or fiberglass may offer a stronger return when matched with complementary finishes. According to remodeling industry data, homeowners can typically expect to recoup around 65 to 70 percent of the project cost in resale value.
In competitive real estate markets, even minor upgrades to curb appeal and usable space can influence buyer interest. Bay windows accomplish both. They contribute to both aesthetic and functional upgrades, which are especially desirable in living rooms, dining areas, and master bedrooms.
How long does installation take?
The installation timeline for a bay window depends on whether the project involves a replacement or a completely new installation. Replacing an existing bay window generally takes 6 to 12 hours. This includes the removal of the old unit, preparation of the opening, setting the new window in place, securing the frame, and completing trim work.
For new installations where a bay window is being added to a flat wall, the process takes longer. This typically requires cutting a new opening, reinforcing the wall structure, adding headers, and building a supporting frame. These jobs can take one to two full days, depending on complexity and weather conditions.
Factors that may extend the timeline include second-story placements, roofing modifications, the addition of window seats, or structural inspections. Working with an experienced contractor and ensuring all materials and permits are ready in advance can help avoid delays.
How do bay windows compare to bow windows in terms of cost and design?
Bay windows are generally less expensive than bow windows due to their simpler design. A standard bay window features three panels: a large central pane flanked by two angled side panes. This structure requires fewer materials and a less complex frame than a bow window, which typically includes four to six equally sized panes forming a gentle curve.
Because of this difference in design, the cost of a bay window often ranges from $2,000 to $4,000, while bow windows tend to start around $3,500 and can exceed $7,000. Labor costs are also higher for bow windows due to the increased installation time and precise framing requirements.
Another consideration is the amount of structural modification involved. Bow windows often require a wider wall opening and more exterior finishing. For homes with limited wall space or structural constraints, bay windows may be more practical and budget-friendly.
In terms of appearance, bay windows create sharp angles and usable interior shelf or bench space, while bow windows offer a smoother, panoramic view. The choice between them should factor in both aesthetics and cost, as well as the architectural compatibility with the home.
When is the best season to install?
The ideal seasons for bay window installation are spring and fall. These periods offer moderate temperatures, stable weather, and better contractor availability. Working conditions during spring and fall are more favorable for tasks such as sealing, caulking, and trimming, which helps ensure long-lasting insulation and weatherproofing.
Summer can also be a suitable time, though higher demand for home improvement projects may lead to longer wait times and potentially higher labor costs. In contrast, winter often comes with discounted rates from contractors looking to fill their schedules, but cold temperatures can make certain installation steps more difficult. Caulking and adhesive materials, for example, may not cure properly in freezing conditions.
Planning the project a few weeks in advance and booking early in the season can help secure better pricing and allow time for permit approvals or material lead times. No matter the season, it is essential to check forecasts and prepare the home’s interior and exterior access areas ahead of time.
Conclusion
Bay window installation costs can vary significantly depending on size, materials, and structural complexity. Understanding the key price drivers and comparing professional quotes helps balance budget and design priorities. Selecting energy-efficient materials and scheduling work during optimal seasons further improves long-term value while enhancing the comfort and appearance of the home.
Get connected with a local window expert today!
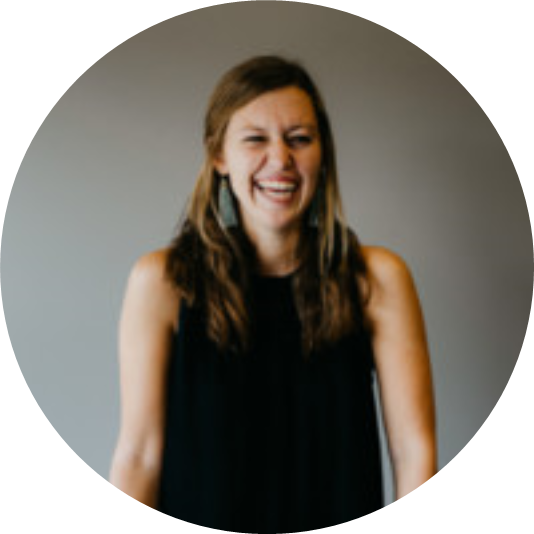
Anna has over six years of experience in the home services and journalism industries and serves as the Content Manager at MyHomePros.com, specializing in making complex home improvement topics like HVAC, roofing, and plumbing accessible to all. With a bachelor’s degree in journalism from Auburn University, she excels in crafting localized, comprehensive guides that cater to homeowners’ unique needs. Living on both coasts of the United States has equipped her with a distinctive perspective, fueling her passion for turning any house into a cherished home through informed, personalized decision-making.